Risk Register and Dust Monitoring: Strengthening Workplace Safety in Australia
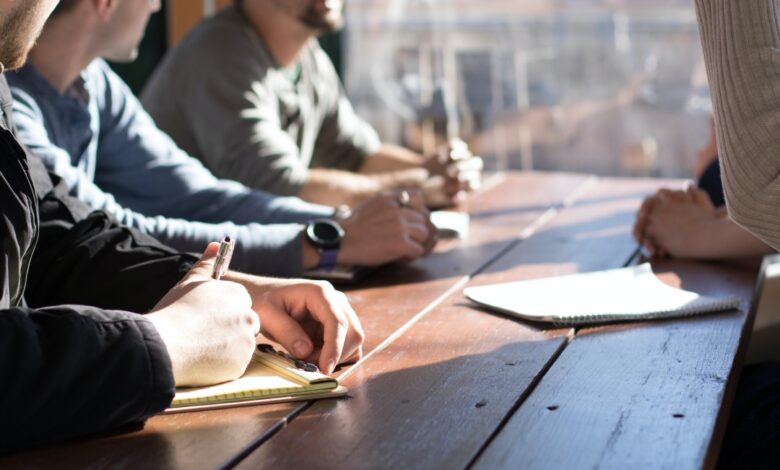
Safety in the workplace in Australia is developing from the routine completion of compliance boxes to one that relies heavily on data and risk management. As “Airborne Dust” is regarded as an effective risk register, industries like construction, mining, manufacturing, and agriculture are beginning to understand its exposure’s long-term health consequences.
When dust monitoring is incorporated into a company’s risk register, the company can manage risks proactively, lower the chances of work-related illnesses, and improve compliance with the strict Australian WHS regulations. In this post, I will argue how Australian companies can strategically manage dust-related risks through a risk register approach to ensure worker safety and regulatory compliance.
The Increasing Problem of Dust Exposure In Australia
While the process of operating machinery and working at heights comes with obvious safety risks, airborne contaminants like silica dust, asbestos fibers, and even combustible dust pose a far more significant threat. That threat tends to be long-term, leading to diseases such as silicosis, lung cancer, and respiratory chronic diseases.
Australia has already made significant movement in the regulation of silica dust exposure, obligating businesses to adopt vigorous dust control procedures. Nonetheless, any progress on mitigating dust risks cannot be done remotely – it must be part of the company’s overarching risk management plan.
Why Dust Monitoring Needs to Be in the Risk Register
A risk register fulfills more than a mere compliance function. This tool aids businesses in effective risk management by:
Identifying potential threats ahead of time.
Implementing controls and evaluating their effectiveness.
Staying abreast with evolving Australian legislation.
Facilitating insights to inform decisions on an operational level.
For industries where dust exposure is an operational risk on a day-to-day basis, placing dust monitoring data in the register guarantees that businesses do not simply comply with WHS legislation, but help avert long-term occupational health issues.
Ways to Add Dust Monitoring into Your Risk Register
1. Risks Associated with Dust Hazards: Steps to Take 127-208
No risk management framework is complete without enumerating the risks of dust exposure in a given workplace. Some overarching questions to ask are:
What kinds of dust exist? (e.g. silica, wood, asbestos, or chemical dust)
What activities produce dust? (e.g. grinding and cutting or even transportation activities)
Who are the most exposed employees? (e.g. machine operators, site personnel, cleaning personnel)
What are the environmental parameters that help diffuse dust? (e.g. degree of ventilation and exposure to wind)
2. Assessing the Risk: Establishing the Relationship between Dust Monitoring Data and Exposure Risks
Dust surveillance systems store and transform data related to particulates, revealing vertical cut position exposure for processes and personnel or sites and times. In order to improve the risk register:
Establish levels of risk (high, medium, low) based on dust monitoring data.
Use Safe Work Australia standards to measure the benchmarked levels of exposure.
Look for patterns as well as areas of concern within the data, such as vicinity of conveyor belts or grinding stations.
By accumulating real-world exposure information, organizations can make effective resource allocation by identifying high risk areas.
3. Activating Control Measures and Assessing Their Effectiveness
After risks have been evaluated, the actions taken to mitigate those risks must also be captured in the risk register. Examples include but are not limited to:
✅ Engineering Controls (Designated areas for specific tasks such as installation, maintenance and service activities. Enclosed workspaces, Ventilation improvements, Dust suppression systems)
✅ Administrative Controls (Improvement in training, Equipment maintenance in routine schedule, Reduction in exposure times)
✅ PPE (Clothing such as masks and filters, Face shields)
Regular Internal Audits should be able to gauge the effectiveness of control measures through assigned review periods. Changes can be made where necessary.
4. Using Devices to Automatically Update the Risk Register
Sophisticated risk management software can now merge the risk register with “real-time” dust monitoring sensors to enable businesses to:
Get notifications when dust levels are so high they are unsafe.
Observe patterns over periods of time and change mitigation approaches to risks based on what needs to be done.
Send instant compliance reports to regulatory authorities.
When the risk register is digitized, businesses shift from monitoring and responding to risks using manual processes to proactively managing identified risks using data.
Complying With Regulations And The Risk Register
Australia WHS regulation is introducing harsher requirements for monitoring occupational exposure to dust. Some of the important compliance requirements are:
Work Health and Safety (WHS) Guidelines: Every company is required to analyze and manage risk of dust exposure and its impact on workers.
Airborne contaminants exposure standards: There are specific limits for the airborne dust such as silica dust and wood dust, among other particulates.
Safe Work Australia’s National Occupational Exposure Database (NOED): Businesses need to keep records and submit reports of risks of exposure.
A risk register that is well-captured and maintained with integration of dust monitoring enables businesses to show compliance proactively rather than suffering penalties, fines, and reputational damages.
Advanced compliance: The business benefits of a proactive risk approach.
There remain organizations whose perception of dust management is merely as a compliance issue instead of a chance for operational excellence. However, risk-taking organizations experience the following:
1. Reduced health risks and long term liabilities
Chronic respiratory diseases develop over time, resulting in expensive compensation claims and legal battles. Preventing exposure today saves businesses from future liabilities.
2. Improved productivity retention of the workers
A healthier work environment leads to:
Reduced sick days off from work due to respiratory problems.
Increased employee engagement and reduced employee attrition.
High operational productivity as dust does not impede various machineries and processes.
3. Enhanced reputation and industry leadership
Organizations who take dust exposure seriously win the trust of employees, regulators, and customers. Monitoring dust exposure by integrating it into the risk register demonstrates leadership in workplace health and sustainability.
The Future of Risk Management: Preventive, Integrated and Smart
The future of managing risk from dust relies heavily on the use of real-time information and predictive analysis. Some emerging trends include:
AI-generated risk registers that monitor exposure data and suggest preventive measures.
Monitors for dust exposure attached to the employee’s body, who then receives personalized risk information.
The integration of other environmental information like weather or air quality index to predict the possibility of risk on certain days.
With proactive risk evaluation and the application of technology, Australian businesses are able to meet preemptive regulatory assessments and ensure that workers are healthy for the long term.
Conclusion: Looking Past Basic Compliance
Incorporating dust monitoring as part of a company’s risk register is not simply trying to comply with regulations; it is an effort toward saving lives, increasing productivity, and ensuring business continuity.
With a systematic risk register that captures real-time exposure data of dust, businesses will be able to:
✅ Know the risks before they manifest.
✅ Take action to decrease exposure to preventable levels.
✅ Maintain compliance to WHS regulations for worksites’ health and safety safeguard.
✅ Build the workplaces that are healthy, safe, and environment-friendly.
In the next few years, effective management of dust risk as proactive measure will be the defining characteristic of Australian businesses that care about their people and also operational efficiency. Now is the perfect time to make that decision.