How to Conduct an Arc Flash Labeling Audit: Ensuring Accuracy and Compliance
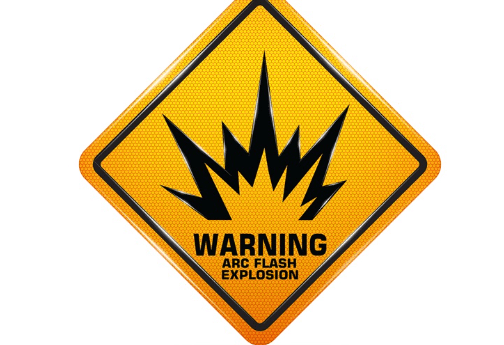
Electrical hazard labeling is an effective way to enhance safety measures that help prevent electrical risks that are a source of harm to employees. The electrical equipment should be appropriately labeled to inform the people who work around them about the risks of arc flash that they may face, and what measures they can take to avoid them.
It is important to have experts comb through your facility and conduct an audit of the arc flash labels to ensure compliance and ensure the safety of your team. This process helps to avoid a situation whereby labels are incorrect, not well placed or do not meet the current standards.
In this article, you will learn about the process of arc flash labeling audits—to make the working area safe and legal.
1. Understand Arc Flash Labeling Requirements
Before planning to conduct an audit, it is required to know the governing codes and regulations related to the arc flash labeling. The information that must be passed across by the label includes but is not limited to arc flash boundary, incident energy, personal protective equipment (PPE) and nominal system voltage. Compliance with these standards gives you the confidence that your facility is implementing standard safety measures.
See also:
2. Check the Current Labels for Their Correctness
The next step in the arc flash labeling audit is the inspection of the existing arc flash labels and their compliance with the regulations. You should ensure that all instruments that are required to have labels have been labeled correctly and the information provided is correct. The incorrect values of incident energy, lack of PPE recommendations, or other issues with the label data may pose threats to workers’ safety.
3. Make Sure That Labels Are Properly Placed
As crucial as the information displayed on the arc flash labels is the placement of those labels. They should be fixed on the outer surface of the electrical equipment in a conspicuous place. They should be long lasting, resistant to the prevailing weather conditions and readable from a fair distance.
Arc flash labels should be provided and affixed to panelboards, switchboards, motor control centers, disconnect switches and other similar equipment. Correct positioning minimizes the probability that the workers will not be able to notice the risks when approaching the equipment.
4. Check for Compliance with Labeling Standards
Ensure that both the information printed on the labels and the labels themselves are current in terms of safety standards. Regular inspections are vital to guarantee that your building stays code-compliant, especially if your electrical system has been updated in some way.
5. Perform Routine Arc Flash Labeling Inspection
Lastly, remember that arc flash labeling is not a one-time job, and the labels should be checked and updated periodically. Electrical systems may evolve; therefore, labels should be updated to reflect the new changes after a certain period. It is recommended to perform a label audit at least once every few years or when a significant electrical system upgrade is planned.